EV Startups Adopt New Approach to Manufacturing
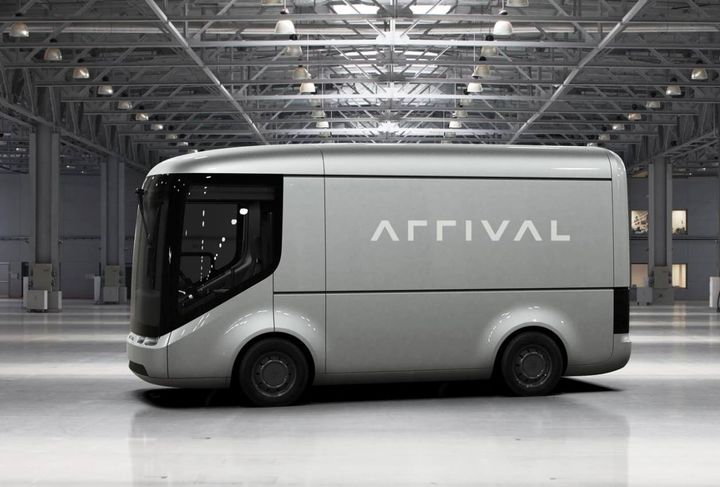
Arrival has decided to build electric van and bus “microfactories” to produce its vehicles.
Arrival
Electric car and van startups seek to avoid Tesla’s manufacturing troubles by taking very different approaches to mass production.
During 2017 and 2018, Tesla struggled to ramp up volume production for its Model 3 sedan. The automaker contended with automation troubles, battery issues and other bottlenecks, and even had to construct a new line in a tent outside its facility to meet production targets. The issues nearly broke the company.
New entrants in the EV game have found better ways to deal with these challenges.
Some companies found investors willing to fork over billions to fund production. Rivian, for instance, raised about $10.5 billion from Amazon, Ford Motor Co. and others to ramp up production of electric vans, pickups and SUVs.
Startups lacking investor support identified other inexpensive paths to mass production.
Usually, automakers spend over $2 billion to build a factory big enough to manufacture 240,000 vehicles or more annually. EV startup, Arrival, has decided to build electric van and bus “micro-factories” instead. These small plants cost $50 million and do not use expensive equipment. Arrival makes its vans out of lightweight colored plastic composite, eliminating the need for paint shops.
Arrival raised around $660 million in a public offering in March. The company used the funds to build two U.S. plants, one in North Carolina devoted to building vans for the United Parcel Service and another in South Carolina producing buses. The company also plans to build a factory in Spain. Arrival’s first micro-factory in Bicester, England, acts as a blueprint for the other plants.
The lack of a paint shop is just one way Arrival keeps production costs down. Its engineers also build molds for plastic body panels. These molds cost thousands of dollars versus millions for traditional metal dies. Engineers have also designed custom molding machines.
The company needs around 70 robots per micro-factory. Arrival purchases commonly used, generic robots from auto industry suppliers like Kuka and Italy’s Comau, which is owned by automaker Stellantis, to do the work.
Arrival’s micro-factory will have one adhesive station and the autonomous wheeled robots will carry a chassis back and forth throughout the assembly process.
The smaller manufacturing facilities can produce 10,000 vans annually per plant rather than 100,000. Each micro-factory will create around 250 jobs.
Electric vehicle maker Canoo has adopted a similar strategy. The company plans to build a mega micro-factory that serves as a hub for smaller future factories.
Electric Last Mile Solutions will launch a small electric van production facility later this year. The company plans to reassemble pre-finished vehicles made in China at a former GM plant in Mishawaka, Indiana, adding new seatbelts and other safety features to meet U.S. regulations. Over time, the company will incorporate more American parts into the vehicles.
Other startups plan to outsource manufacturing to trim production costs. Contract manufacturing deals reduce upfront costs with partnering companies later taking a cut of revenue and potential profits.
REE Automotive Holding entered agreements with American Axle and Mitsubishi Motors to build its electric platforms for delivery vehicles and people movers at scale. While REE and Fisker have teamed up with Magna International to build EVs. Fisker also has a similar agreement with Foxconn Technology.